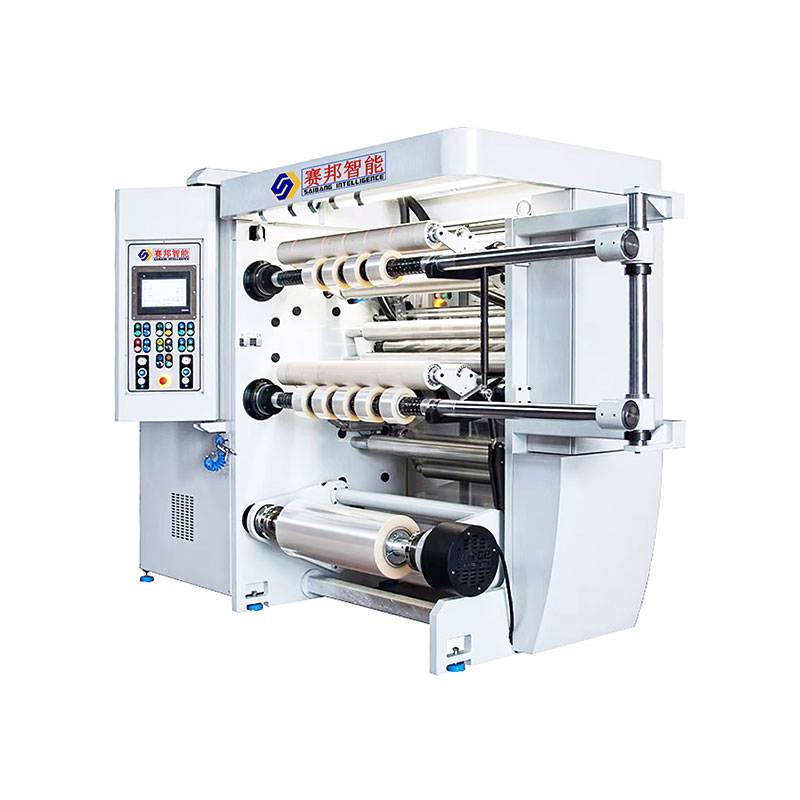
Plastic Film Slitting Machine is a mechanical device used to accurately slit wide plastic film materials according to preset specifications and sizes. It unwinds the wide raw material through the unwinding device, cuts it according to the set width through the slitting device, and then rewinds the slit narrow film into a roll through the rewinding device to meet the requirements of different industries for plastic film specifications. It plays a vital role in the fields of plastic processing, packaging material production, etc.
Plastic Film Slitting Machine parameter
Model: | FQ-16A |
Brand: | Saibang Intelligence |
Adaptation Materials: | Film, Laminated Film, Puffing Paper, Air-Laid Paper, Laminated Paper, Etc. |
Material Width: | 1600mm |
Mechanical Speed: | 300-800m/min |
Unwinding Diameter: | Φ800mm |
Winding Diameter: | Φ500mm |
OEM: | OEM/ODM |
Plastic Film Slitting Machine features
High-precision servo drive: With its excellent servo drive technology and high-precision servo motor, the Plastic Film Slitting Machine can achieve micron-level slitting accuracy. Its servo system has fast response speed and high control accuracy, which can control the speed synchronization error of the whole machine within a very small range, ensuring the precise matching of the speeds of unwinding, slitting, and rewinding in the production process. For example, when running at high speed (the mechanical speed can reach 300-800m/min), it can still ensure that the speed deviation of each part does not exceed ±0.5%, avoiding problems such as material stretching, deformation or wrinkles caused by inconsistent speed, greatly improving the accuracy and stability of slitting, and ensuring the consistency of product quality.
Modular design: The Plastic Film Slitting Machine adopts a modular design, and each functional module is relatively independent and cooperates with each other. This design makes it easy to flexibly configure and expand the equipment according to different production needs, and can quickly adapt to various production environments. Taking the material width as an example, the material width it can adapt to is up to 1600mm. By replacing or adjusting the module, it can easily cope with the slitting tasks of materials of different specifications. At the same time, the modular design also facilitates the transportation, installation and maintenance of the equipment. When a module fails, the module can be replaced separately, which greatly shortens the maintenance time and reduces the maintenance cost. The general module replacement time can be controlled within 2 hours.
Advanced cutting system: The Plastic Film Slitting Machine is equipped with high-precision cutting tools and advanced control algorithms, which can achieve accurate cutting of plastic films. The cutting width error can be controlled within ±0.1mm, and the cutting edge is smooth and neat, without burrs or delamination. For example, for ultra-thin plastic films with a thickness of 0.02mm, accurate slitting can also be achieved to ensure that the slitting film meets strict size requirements. During the cutting process, the tool's running trajectory and cutting force can be accurately controlled, avoiding material waste and product quality problems caused by inaccurate cutting, and the material loss rate can be reduced to less than 1%.
Adapt to a variety of material characteristics: The Plastic Film Slitting Machine has an advanced tension adjustment function, which can flexibly adjust the tension of the film during the slitting process according to the characteristics and thickness of different plastic film materials. The tension adjustment range is 0 - 50N, and the adjustment accuracy can reach ±0.5N. Through real-time monitoring and feedback control, the film can maintain stable tension throughout the slitting process to avoid problems such as material stretching deformation caused by excessive tension or material wrinkling and deviation caused by too little tension. For example, for thinner and more elastic PE films, the tension can be accurately controlled at 5 - 10N; for thicker and harder PET films, the tension can be adjusted to 20 - 30N to ensure the stability and consistency of slitting quality. In addition to film cutting, it is also suitable for precise slitting of various materials such as various types of paper and composite materials.
Convenient and efficient operation: Plastic Film Slitting Machine adopts a digital human-machine interface, which is simple and convenient to operate. The operator can understand the equipment operation status, production parameters and other information in real time through the intuitive interface, and perform convenient parameter settings and adjustments. The interface has fault diagnosis and alarm functions, which can promptly detect equipment operation problems and provide solutions. When the equipment fails, the interface will display the fault code and fault location within 1 second, and send out sound and light alarm signals to remind the operator to deal with it in time. In addition, operators can also query historical production data through the interface, such as production quantity, production time, fault records, etc., to provide strong support for production management, improve the level of production automation and the work efficiency of operators.
Low-noise operation: Noise control factors are fully considered during the design and manufacturing of the equipment. The use of low-noise transmission components and optimized mechanical structure effectively reduces the noise level of the equipment during operation. When the equipment is running at full load, the noise value can be controlled below 70 decibels, which is significantly lower than that of similar equipment. In the production workshop, the noise of the equipment during operation is significantly reduced, providing operators with a relatively quiet and comfortable working environment, which is conducive to improving the work efficiency and physical and mental health of operators.
Packaging material industry: Plastic film is an important component of packaging materials and is widely used in the packaging of food, medicine, daily necessities and other products. Plastic film slitting machines can slit wide film materials into narrow films of different specifications for making various packaging bags, packaging films, etc. For example, in the field of food packaging, the slit films can be used to make snack packaging bags, beverage packaging films, etc. to meet the packaging needs of different products. For some foods that require high packaging sealing, such as cakes and meat products, plastic films with a thickness of 0.03-0.05mm can be used for slitting and packaging, which effectively extends the shelf life of food.
Printing industry: During the printing process, wide plastic films need to be slit into specifications suitable for printing. The slit films can be used to print various patterns, texts, etc., and are widely used in printing fields such as advertising, labels, and packaging. For example, in label printing, the slit films can be used to make product labels, logistics labels, etc. According to different printing requirements, the film can be slit into narrow films with a width of 20-100mm, and the printing accuracy can reach more than 600dpi, ensuring clear printed patterns and bright colors.
Electronics industry: With the continuous development of electronic products, the demand for plastic films is also increasing. Plastic film slitting machines can cut out film materials that meet the requirements of the electronics industry, which are used to make insulating materials, protective films, etc. for electronic products. For example, in circuit board manufacturing, the slit film can be used to cover the circuit board to play an insulating and protective role. For some high-precision electronic products, such as mobile phones and tablets, ultra-thin plastic films with a thickness of 0.01-0.02mm can be used as protective films to ensure the normal operation of electronic products.
Agricultural field: In agriculture, plastic films are widely used in greenhouses, ground film coverings, etc. The slit films can be made into greenhouse films, ground films, etc. of different specifications according to different agricultural needs. For example, in greenhouses, the slit films can be used to cover the greenhouses, adjust the temperature and humidity, and promote the growth of crops. According to the size of the greenhouse and the needs of the crops planted, the film can be slit into wide films with a width of 4-12m. The thickness can be selected from 0.05-0.2mm according to the use environment. It has good light transmittance, heat preservation and aging resistance.
Medical industry: The medical field has high requirements for the hygiene and safety of plastic films. The slit film can be used to make medical packaging materials, surgical dressings, etc. For example, in drug packaging, the slit film can be used to package drugs to ensure the quality and safety of drugs. Medical packaging materials usually use aseptic slitting technology to ensure that the film is not contaminated during the slitting process. At the same time, the thickness and strength of the film must meet the relevant standards of the medical industry, such as the thickness is generally 0.03-0.1mm, and the tensile strength is not less than 20MPa.
Plastic Film Slitting Machine maintenance
Daily cleaning: After production every day, the surface of the equipment should be wiped with a clean soft cloth to remove dust, oil and other impurities. For electrical control cabinets, dry compressed air should be used to blow to prevent dust from entering and affecting the normal operation of electrical components. At the same time, the debris and waste inside the equipment should be cleaned regularly to prevent clogging of transmission parts and affecting the accuracy of the equipment. It is generally recommended to perform a comprehensive cleaning at least once a week.
Regular lubrication: According to the requirements of the equipment lubrication chart, the various lubrication points of the equipment should be lubricated regularly. For transmission parts such as gears and chains, suitable lubricating grease should be used, such as No. 2 lithium-based grease, and refueling should be done every 200-300 hours; for high-speed running parts such as bearings, lubricating oil should be used for lubrication, such as No. 32 turbine oil, and refueling should be done every 100-150 hours. When refueling, pay attention to the moderate amount of oil, avoid too much or too little, so as not to affect the lubrication effect and equipment operation.
Inspection and replacement of wearing parts: Regularly check the use of wearing parts of the equipment, such as cutting tools, bearings, belts, seals, etc. Cutting tools should be sharpened or replaced in time according to the usage. Generally, when the blade wear exceeds 0.2mm, it should be sharpened; when the wear exceeds 0.5mm, a new tool should be replaced. The bearing should be checked for smooth operation and abnormal noise. If there is a problem, it should be replaced in time. The belt should be checked for tension and wear. When the belt is loose or severely worn, the tension should be adjusted or replaced in time. The sealing performance of the seal should be checked regularly. If there is leakage, it should be replaced in time.
Electrical system maintenance: Regularly check whether the connection lines of the electrical system are loose or aging, and whether the electrical components are working properly. Perform a comprehensive inspection of the electrical system at least once a month, including the detection of power supply voltage and current, and the performance test of components such as controllers and sensors. If electrical components are found to be damaged or the performance is degraded, they should be replaced in time. At the same time, keep the electrical control cabinet dry and clean to avoid moisture and dust.
Equipment calibration: Calibrate the equipment regularly to ensure the operating accuracy and stability of the equipment. The calibration content includes parameters such as cutting width, tension, and speed. Generally, a comprehensive calibration is performed once a quarter. Professional calibration tools and equipment should be used for calibration, and the operation should be carried out in accordance with the equipment's operating manual. After calibration, a trial run should be carried out to check the equipment's operation. If there are any problems, adjustments should be made in a timely manner.
Operation environment maintenance: Keep the equipment's operating environment dry, ventilated, and dust-free. Avoid corrosive gases and liquids around the equipment, the ambient temperature should be controlled at 5 - 40°C, and the relative humidity should not exceed 80%. If the ambient humidity is too high, dehumidification measures should be taken; if the ambient temperature is too high, ventilation and heat dissipation should be strengthened. At the same time, debris around the equipment should be cleaned regularly to keep the equipment's operating channels unobstructed.
Operator training: Operators should be trained regularly to familiarize them with the equipment's operating procedures and maintenance methods. The training content includes equipment startup, shutdown, parameter setting, troubleshooting, etc. Operators should undergo professional training and pass the assessment before they can take up their posts.
Establish maintenance files: Establish equipment maintenance files to record the equipment's maintenance time, maintenance content, replacement of wearing parts, and other information. Through the maintenance files, you can understand the equipment's operating status and maintenance status, and provide a basis for equipment repair and replacement. At the same time, maintenance records can also help analyze the causes of equipment failures, take corresponding preventive measures, and reduce the occurrence of equipment failures.
Foshan Saibang Intelligent Equipmemt Co., Ltd. is located in nanhai District, an important industrial town in Guangdong Province, is a research and development, manufacturing, sales in one of the National High-tech Enterprise. The founding team of the company has been deeply engaged in the new material industry for 15 years, and is committed to the R&D, manufacturing and technical integration of special equipment for the new material & medical and eisai special equipment, providing systematic solutions and technical services for customers. We have over 30 independent intellectual property rights, and after years of experience accumulation, we currently has customers all over the country, Southeast Asia, Europe, and South America.Our products include casting/laminating equipment, coating machine, non-woven special equipment, all kinds of non-standard automation equipment and related mechanical and electrical accessories.
We adhere to the development philosophy of "technology leading, quality winning, service first, and win-win cooperation", with continuous research and development power for the industry to push technical equipment of cutting edge, with stable quality based on competitive global market, with sincere technology service realize the value of customer demand.