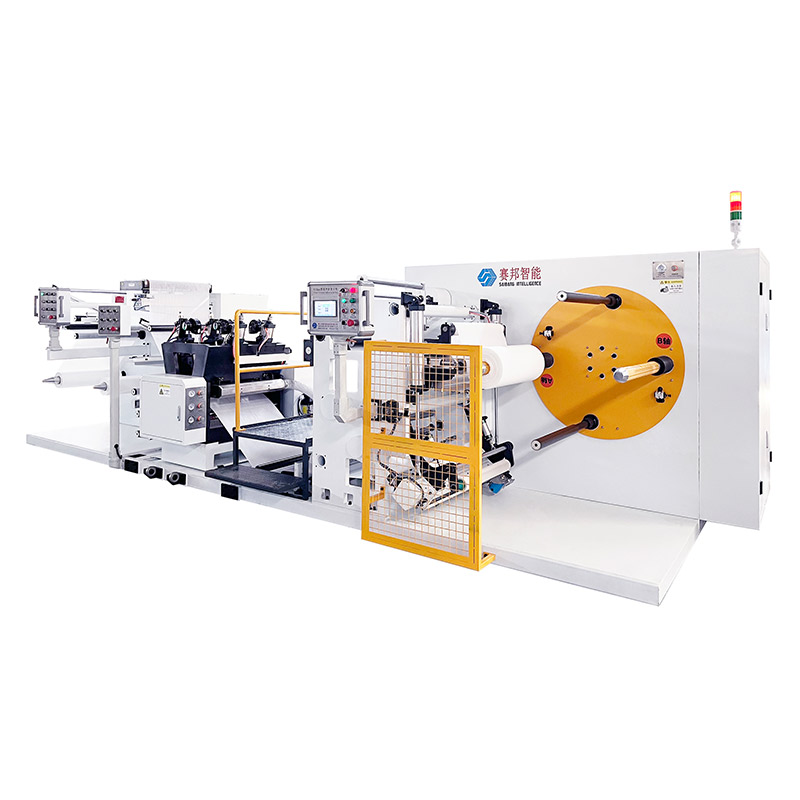
The Automatic Laminating Machine integrates a one-stop solution from substrate unwinding to ultrasonic lamination, main control system regulation, edge trimming and rewinding, as well as a full servo electronic control system, aiming to meet the market's diversified needs for substrate fabrics for various types of sanitary products and protective products.
650mm Ultrasonic Automatic Laminating Machine parameter
Model: | SFH65A |
Brand: | Saibang Intelligence |
Adaptation Materials: | Hot Air Nonwoven, Spunbonded Nonwoven |
Material Width: | 650mm |
Mechanical Speed: | 80m/min |
Normal Speed: | 50-80m/min (Depending On Material And Pattern) |
Finished Product Width: | 600mm |
Effictive Embossing Width: | 630mm |
Unwinding Diameter: | Φ800mm |
Winding Diameter: | Φ800mm |
OEM: | OEM/ODM |
650mm Ultrasonic Automatic Laminating Machine features
Efficient lamination capability: This automatic laminating machine has a strong lamination capability and can efficiently laminate a variety of substrates such as hot air nonwoven and spunbonded nonwoven. Its mechanical speed can reach 80m/min, and under normal production conditions, the speed range is between 50-80m/min (the specific speed depends on the material and pattern). This efficient lamination capability enables enterprises to produce a large number of composite materials in a short time to meet market demand.
Accurate size control: The machine width is 650mm, the finished product width is 600mm, and the effective embossing width is 630mm. This precise size control ensures the quality and specification consistency of the composite material. During the production process, the machine can accurately laminate and emboss the substrate according to the preset width, avoiding quality problems caused by dimensional deviation.
Large roll diameter processing capability: The unwinding diameter and the rewinding diameter are both Φ800mm. This large roll diameter processing capability allows the machine to process more substrates at one time, reducing the frequency of roll changes and improving the continuity and stability of production. For some large-scale production enterprises, the large roll diameter processing capacity can reduce production costs and improve production efficiency.
Full servo electronic control system: The machine is equipped with a full servo electronic control system with high precision, high response speed and good dynamic performance. The full servo system can accurately control the machine's operating speed, tension and compounding pressure and other parameters according to different substrate materials and compounding requirements. For example, when compounding materials of different thicknesses, the full servo system can automatically adjust the compounding pressure to ensure stable compounding quality.
Support pattern customization: The automatic compounding machine supports pattern customization. The composite materials produced are not only excellent in strength, but also can be efficiently produced whether it is a flat or 3D pattern. Through advanced ultrasonic compounding technology and precise pattern positioning system, the machine can accurately compound different patterns onto the substrate to meet the market demand for personalized products.
Sanitary products industry: In the sanitary products industry, automatic laminating machines are widely used in the production of diapers, sanitary napkins and other products. Diapers need to be compounded with a variety of substrates, such as non-woven fabrics, absorbent materials, etc. Automatic laminating machines can efficiently compound these substrates together to form diaper substrates with good water absorption and breathability. At the same time, supporting pattern customization can meet consumers' personalized needs for the appearance of diapers. In the production of sanitary napkins, automatic laminating machines can compound non-woven fabrics and sanitary napkin cores to improve the absorption capacity and comfort of sanitary napkins.
Protective products industry: Protective clothing and surgical gowns and other protective products have high requirements for the strength and protective performance of materials. Automatic laminating machines can compound a variety of non-woven fabrics with protective properties to form protective product substrates with high strength and good protective performance. For example, when producing protective clothing, non-woven fabrics of different materials can be compounded together to improve the protection level and durability of protective clothing.
Medical supplies industry: In addition to protective products, automatic laminating machines can also be used in the production of some medical products, such as medical dressings, surgical kits, etc. Medical dressings require soft and breathable materials. Automatic laminating machines can compound non-woven fabrics and other materials to form a dressing substrate that meets medical requirements. Various materials in surgical kits can also be compounded by automatic laminating machines to improve the quality and performance of surgical kits.
Home furnishings industry: In the home furnishings industry, automatic laminating machines can be used to produce some home furnishings with special functions, such as dustproof cloth, sound insulation materials, etc. By compounding different non-woven fabrics, home furnishings can be given better performance and functions. For example, dustproof cloth can be compounded with non-woven fabrics of different materials to improve its dustproof effect and durability.
Industrial supplies industry: In the industrial supplies industry, automatic laminating machines can be used to produce some industrial supplies with special properties, such as filter materials, insulation materials, etc. Filter materials need to have good filtering performance and strength. Automatic laminating machines can compound multiple materials together to form filter materials that meet industrial requirements. Insulating materials need to have good insulation performance and stability. Automatic laminating machines can produce high-quality insulation materials through precise control and compounding processes.
650mm Ultrasonic Automatic Laminating Machine maintenance
Daily cleaning: After the production is finished every day, the machine should be thoroughly cleaned. Use a clean rag to wipe the surface of the machine to remove dust, paper scraps and other debris. In particular, key parts such as the composite roller and trimming knife should be carefully cleaned to avoid debris accumulation affecting the composite quality and machine operation. At the same time, clean the paper scraps and dust inside the machine to keep the inside of the machine clean. You can use tools such as vacuum cleaners to clean up the debris inside the machine.
Lubrication and maintenance: Regularly lubricate and maintain the various moving parts of the machine. According to the machine's instruction manual, select appropriate lubricants to lubricate bearings, gears, chains and other components. For example, lubricate bearings once a week and lubricate gears and chains once a month. Lubrication can reduce friction between components, reduce wear and extend the service life of the machine. When lubricating, pay attention to the amount of lubricant and the application position to ensure good lubrication effect.
Component inspection and replacement: Regularly check the various components of the machine, such as composite rollers, trimming knives, sensors, etc. If the components are found to be severely worn or malfunctioning, they should be replaced in time. For example, if the surface of the composite roller is worn or scratched, it will affect the composite quality, and a new composite roller should be replaced in time. At the same time, when replacing parts, follow the correct operating method to ensure that the parts are firmly installed to avoid failures that affect the normal operation of the machine.
Electrical system inspection: Regularly check the electrical system of the machine, including motors, sensors, controllers and other components. Check the operation of the motor. If the motor has abnormal sounds or heat, stop the machine for inspection in time. Check the sensitivity and accuracy of the sensor to ensure that the sensor can work properly. At the same time, check whether the controller is set correctly to avoid electrical failures that affect the normal operation of the machine. Professional electrical testing equipment can be used to conduct a comprehensive inspection of the electrical system.
Tightening of mechanical parts: During the operation of the machine, some mechanical parts may become loose due to vibration and other reasons. Regularly check the various mechanical parts of the machine, such as bolts, nuts, bearing seats, etc. If looseness is found, tighten them in time. When tightening, operate according to the specified torque to avoid affecting the performance of the machine due to excessive or insufficient tightening.
Storage environment: When the machine is not used for a long time, it should be stored in a dry, ventilated, non-corrosive gas environment. Avoid moisture, rust or corrosion of corrosive gases. At the same time, cover the surface of the machine with a dust cover to prevent dust and debris from entering the machine. During storage, the machine should be inspected and maintained regularly to ensure that the machine is in good condition.
Training operators: Provide professional training for operators to familiarize them with the operation methods and maintenance knowledge of the machine. Operators should strictly follow the operating procedures to avoid damage to the machine due to improper operation. At the same time, operators should regularly perform simple inspections and maintenance on the machine, such as cleaning the surface dust, checking the tightness of components, etc., to promptly discover and solve small problems with the machine to avoid problems from expanding.
Foshan Saibang Intelligent Equipmemt Co., Ltd. is located in nanhai District, an important industrial town in Guangdong Province, is a research and development, manufacturing, sales in one of the National High-tech Enterprise. The founding team of the company has been deeply engaged in the new material industry for 15 years, and is committed to the R&D, manufacturing and technical integration of special equipment for the new material & medical and eisai special equipment, providing systematic solutions and technical services for customers. We have over 30 independent intellectual property rights, and after years of experience accumulation, we currently has customers all over the country, Southeast Asia, Europe, and South America.Our products include casting/laminating equipment, coating machine, non-woven special equipment, all kinds of non-standard automation equipment and related mechanical and electrical accessories.
We adhere to the development philosophy of "technology leading, quality winning, service first, and win-win cooperation", with continuous research and development power for the industry to push technical equipment of cutting edge, with stable quality based on competitive global market, with sincere technology service realize the value of customer demand.