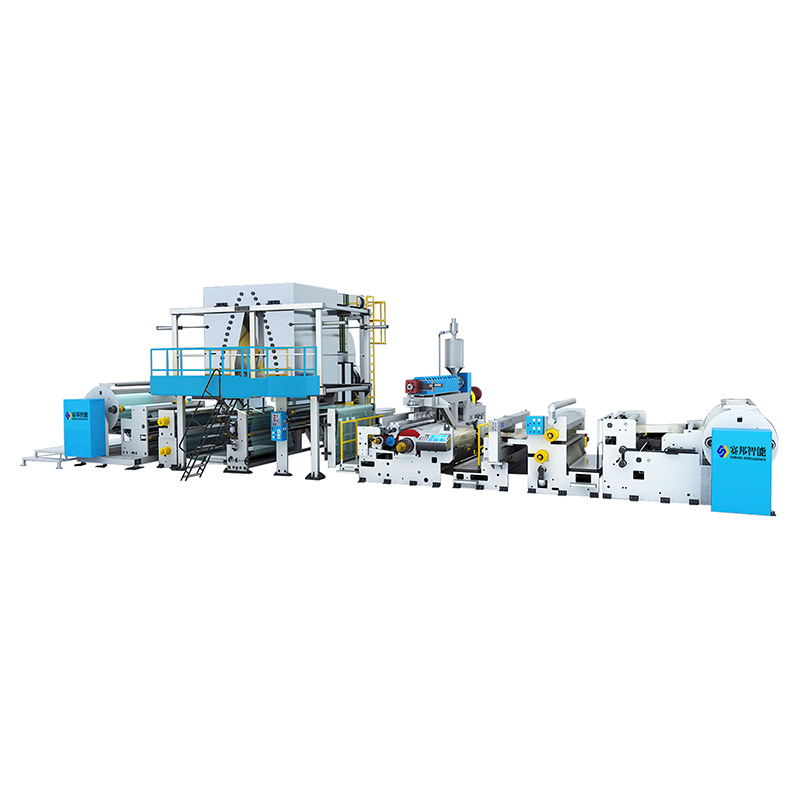
Extrusion Coating Lamination Machine is an advanced industrial equipment designed for compounding one or more layers of materials through extrusion coating process. It uses high-temperature molten plastic (such as polyethylene, polypropylene, etc.) as adhesive, and heats, melts and extrude plastic particles into a uniform film through the screw system of the extruder. Then, the molten plastic is evenly coated on the surface of the substrate (such as paper, aluminum foil, non-woven fabric, plastic film, etc.) through a specific coating head, and then another layer of substrate is closely attached to the coated substrate through a composite roller to form a new material with composite properties.
Extrusion Coating Lamination Machine parameter
Model: | SJC24 |
Brand: | Saibang Intelligence |
Adaptation Materials: | Suitable For Soft Packaging Of Food And Drugs, Special Aluminum Plastic Film For Battery Packaging, Pre Coating Film, Paper Cup Coating Film, Tetra Pak Packaging,non-Woven Fabric Coating,etc. |
Substrate Width: | 1100-2400mm |
Machine Design Speed: | 150-300m/min |
Features: | Double Station Unwinding And Rewinding With High Speed Automatic Splicing. Single And Double-Sided Coating Laminating. |
OEM: | OEM/ODM |
Extrusion Coating Lamination Machine features
High-precision coating control:
Coating thickness control accuracy: With the advanced closed-loop control system, the coating thickness control accuracy can reach ±1μm, ensuring the stability and consistency of product quality.
Coating width uniformity: Through precise coating head design and fluid mechanics optimization, the coating width uniformity error is less than 2%, effectively avoiding material waste and performance degradation caused by uneven coating.
Efficient production capacity:
Design speed: The machine design speed is as high as 150-300m/min, far exceeding traditional coating equipment, significantly improving production efficiency.
Double-station unwinding and rewinding: Equipped with a high-speed automatic connection double-station unwinding and rewinding system, it realizes continuous production without stopping, reduces production interruption time, and further improves production capacity.
Excellent composite strength:
Composite strength test: After rigorous testing, the peel strength of the composite product of this machine can reach 3-8N/15mm (the specific value depends on the material combination), which is much higher than the industry standard, ensuring the long-term stability and reliability of the composite material.
Multi-layer composite capability: supports single-sided and double-sided coating composite, which can be flexibly adjusted according to customer needs to meet the performance requirements of different application scenarios.
Convenient and safe operation:
Digital human-machine interface: adopts an intuitive and easy-to-use touch screen operation interface, all parameters can be displayed and adjusted in real time, and operators can quickly get started without complex training.
Safety protection mechanism: built-in multiple safety protection mechanisms, such as emergency stop button, overload protection, abnormal temperature alarm, etc., to ensure the safety of operators and stable operation of equipment.
Easy maintenance and maintenance:
Modular design: The machine adopts modular design, and each component is easy to disassemble and replace, which reduces maintenance costs and time.
Automatic lubrication system: equipped with automatic lubrication system to ensure good lubrication status of key components and extend the service life of the equipment.
Environmental protection and energy saving:
Energy-saving design: by optimizing the heating system and cooling system, energy consumption is reduced, and energy saving is about 20% compared with traditional equipment.
Waste recycling: equipped with waste recycling device, the waste generated in the production process is recycled and reused, which reduces production costs and conforms to the concept of green production.
Flexible packaging for food and medicine:
High barrier packaging: Using extrusion composite coating technology, plastic film with high barrier properties is composited with paper or aluminum foil to make packaging materials with excellent barrier properties, effectively extending the shelf life of food and medicine.
Easy-tear design: By precisely controlling the coating thickness and composite process, an easy-tear design can be formed on the packaging material, making it convenient for consumers to open the package.
Special aluminum-plastic film for battery packaging:
Battery safety protection: Aiming at the special needs of battery packaging, an aluminum-plastic film with excellent chemical corrosion resistance, high temperature resistance and insulation performance is developed to provide all-round safety protection for the battery.
Lightweight design: By optimizing the material combination and composite process, the lightweight design of aluminum-plastic film is realized, which reduces the overall weight of the battery and increases the energy density of the battery.
Pre-coated film and paper cup paper:
Pre-coated film production: The pre-coated film is coated on the surface of the paper to give the paper waterproof, oil-proof, wear-resistant and other properties, which are widely used in printing, packaging and other fields.
Paper cup paper manufacturing: Using extrusion composite coating technology, plastic film with heat-sealing properties is composited with paper to make heat-sealable paper cup paper, which improves the convenience and hygiene of paper cups.
Tetra Pak packaging:
Multi-layer composite structure: Through the multi-layer composite process, paper, aluminum foil and plastic film are tightly combined to form Tetra Pak packaging materials with excellent barrier properties and mechanical strength, which are widely used in the packaging of liquid foods.
Environmentally friendly and recyclable: Tetra Pak packaging materials can be recycled and reused, meet environmental protection requirements, and reduce the impact on the environment.
Non-woven fabrics:
Functional coating: Plastic films with specific functions (such as antibacterial, waterproof, breathable, etc.) are coated on the surface of non-woven fabrics to give non-woven fabrics new functional characteristics, which are widely used in medical, health, home and other fields.
Composite reinforcement: Through the composite process, non-woven fabrics are composited with other materials (such as plastic films, paper, etc.) to improve the strength and durability of non-woven fabrics.
Extrusion Coating Lamination Machine maintenance
Daily cleaning:
Regular cleaning: After the production is completed every day, the surface of the machine should be cleaned to remove dust, oil and other debris to keep the machine clean.
Key cleaning of key parts: Key parts such as coating head, composite roller, unwinding and rewinding system should be cleaned to ensure the normal operation of the equipment.
Lubrication and maintenance:
Regular lubrication: According to the requirements of the equipment manual, lubricate the moving parts of the machine regularly to ensure good lubrication.
Lubricant selection: Choose the appropriate lubricant brand and model to avoid using inferior lubricants to cause equipment damage.
Component inspection and replacement:
Regular inspection: Regularly check the various components of the machine, such as whether the screws are loose, whether the belts are worn, whether the electrical components are aging, etc., to find and deal with problems in time.
Timely replacement: Severely worn or damaged parts should be replaced in time to avoid affecting the normal operation of the equipment and production quality.
Electrical system maintenance:
Moisture and dustproof: Keep the electrical control cabinet dry and clean to avoid moisture and dust from damaging the electrical components.
Regular inspection: Regularly inspect and test the electrical system to ensure the normal operation and safety of the electrical components.
Safety operation specifications:
Operation training: Provide professional operation training to operators to ensure that they are familiar with the performance, operation methods and safety precautions of the equipment.
Compliance with regulations: Operators should strictly abide by the safety operation regulations of the equipment and shall not operate in violation of regulations or change equipment parameters without authorization.
Regular professional maintenance:
Professional maintenance team: Establish a professional maintenance team to conduct comprehensive inspection and maintenance of the equipment on a regular basis to ensure the long-term stable operation of the equipment.
Maintenance records: Keep detailed records of each maintenance, including maintenance time, maintenance content, replacement parts and other information for subsequent tracking and management.
Foshan Saibang Intelligent Equipmemt Co., Ltd. is located in nanhai District, an important industrial town in Guangdong Province, is a research and development, manufacturing, sales in one of the National High-tech Enterprise. The founding team of the company has been deeply engaged in the new material industry for 15 years, and is committed to the R&D, manufacturing and technical integration of special equipment for the new material & medical and eisai special equipment, providing systematic solutions and technical services for customers. We have over 30 independent intellectual property rights, and after years of experience accumulation, we currently has customers all over the country, Southeast Asia, Europe, and South America.Our products include casting/laminating equipment, coating machine, non-woven special equipment, all kinds of non-standard automation equipment and related mechanical and electrical accessories.
We adhere to the development philosophy of "technology leading, quality winning, service first, and win-win cooperation", with continuous research and development power for the industry to push technical equipment of cutting edge, with stable quality based on competitive global market, with sincere technology service realize the value of customer demand.