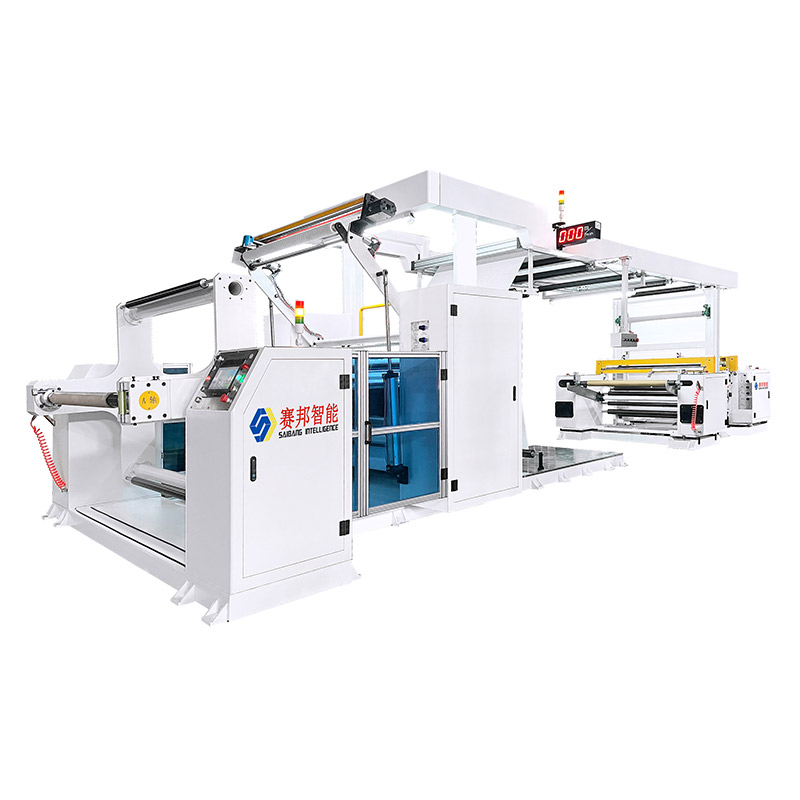
Non Woven Fabric Lamination Machine is a highly efficient production equipment specially used to laminate different types of substrates and materials. It is mainly composed of substrate unwinding device, laminating device, host control system and trimming and winding device, etc., which can efficiently complete the laminating process of various non-woven fabrics and sanitary materials.
1200mm Non Woven Fabric Lamination Machine parameter
Model: | SFH12A |
Brand: | Saibang Intelligence |
Adaptation Materials: | Nonwoven Fabric And Other Sanitary Materials |
Machine Width: | 1200mm |
Max Design Speed: | 100m/min |
Normal Speed: | 90m/min |
Effective Roller Surface Width: | 1200mm |
Unwinding Diameter: | 1st: Φ1000mm; 2nd: Φ1000mm |
Winding Diameter: | Φ1300mm |
OEM: | OEM/ODM |
1200mm Non Woven Fabric Lamination Machine features
High-efficiency composite speed and stability: The maximum design speed of Non Woven Fabric Lamination Machine is 100m/min, and the normal speed is 90m/min. Hot Press technology enables the machine to complete composite processing in a short time. The equipment can run at high speed, and the composite quality is stable, which is suitable for large-scale production. Since the hot pressing process can quickly heat and apply pressure, the substrates such as non-woven fabrics can be quickly combined to meet the rhythm of high-demand production lines.
Temperature control range: 150°C-200°C. Through hot pressing technology, the equipment can achieve high-precision temperature control. The temperature during each composite process is precisely adjustable to ensure that the temperature remains within the ideal range, so that different types of non-woven fabrics and other materials can be composited in the best thermal environment.
Pressure control system: adjustable pressure range The equipment is equipped with a precise pressure control system, which can adjust the required pressure according to different materials and composite requirements. Under high pressure, the materials can be tightly combined, enhancing the mechanical strength of the composite product.
Enhance the mechanical properties of composite materials: Through hot pressing technology, the combination between composite materials becomes tighter. The effect of high temperature and high pressure makes the molecular structure fuse at the composite interface, thereby greatly improving the physical properties of the product such as tensile strength, tear resistance, and wear resistance. This is especially important for non-woven materials that need to withstand high mechanical stress, such as medical protective clothing and surgical gowns. In addition, hot pressing can ensure consistency in each composite process, reduce quality differences caused by temperature or pressure fluctuations, and make the quality of the final product more stable.
High-quality surface quality: The use of hot pressing technology can effectively eliminate bubbles, wrinkles or uneven phenomena that may occur during the composite process. High temperature and high pressure make the surface of the composite material smoother and smoother, ensuring the appearance quality of the product. Since hot pressing can fully fuse the surface of the substrate, the joints between the composite materials are tighter, reducing problems such as leakage and breakage caused by joint problems.
High energy efficiency and environmental protection: efficient energy utilization The energy utilization efficiency of hot pressing technology is very high. During the hot pressing process, through rapid heating and precise heat transfer, the required composite temperature can be quickly reached without wasting energy. This makes the entire production process not only efficient but also energy-saving. Since no additional adhesives or chemical glues are required during the hot pressing process, the use of chemicals is reduced, which meets environmental protection requirements. This is especially important for industries that require green production, such as the manufacture of medical and health products.
Wide applicability: Applicable to a variety of materials Hot pressing technology has high adaptability and can handle various types of non-woven fabrics, films, paper, metal foils and other materials. Whether it is producing light and thin protective clothing materials or heavy medical fabrics, hot pressing technology can provide ideal composite effects.
Flexible specification adjustment: The equipment supports the composite of substrates of different sizes. Its effective roller width is 1200mm, which is suitable for non-woven fabrics and sanitary materials of different thicknesses and widths, and can flexibly respond to diverse production needs.
Automated control system: Equipped with an advanced automated control system, the operator can accurately adjust parameters such as temperature, pressure and speed during the composite process through an intelligent interface. All operations during the hot pressing process are automatically controlled by the system, reducing human errors and ensuring the consistency of composite quality.
Real-time data monitoring and analysis: The system is also equipped with real-time data monitoring functions, which can record key data such as temperature, pressure, speed, etc. in each production link. Operators can view various parameters in the production process in real time to ensure stable operation of the equipment and make timely adjustments.
Non-woven fabric production field: Non-woven fabric is a widely used material in modern industry, especially in the sanitation, medical, filtration and other industries. Non Woven Fabric Lamination Machine can composite different types of non-woven fabric substrates with other materials, and is widely used in non-woven fabric production lines for the production of various protective clothing, medical dressings, diapers and other sanitary products.
Production of personal hygiene products: When producing diapers, sanitary napkins and other personal hygiene products, the composite machine can efficiently composite various substrates, including non-woven fabrics, films, paper and other different materials. Through precise control of the composite process, it can ensure stable and qualified product quality, improve production efficiency, and reduce production costs.
Medical and health field: In the medical industry, especially in the production of medical supplies such as surgical gowns and protective clothing, the equipment provides an efficient and stable composite solution. By composite different non-woven fabrics and other protective materials, high-performance medical products can be produced to meet the needs of hospitals and medical institutions.
Production of filter materials: Non Woven Fabric Lamination Machine is not only suitable for the production of sanitary products, but also widely used in the production of various filter materials. The composite of non-woven fabrics and other special materials can effectively improve the filtering effect and is widely used in many fields such as air, water treatment, and oil filtration.
Production of environmentally friendly materials: With the improvement of environmental awareness, many companies have begun to use degradable and reusable environmentally friendly materials to replace traditional synthetic materials. This composite function can efficiently composite different environmentally friendly substrates to produce various products that meet environmental standards and meet the market demand for environmentally friendly materials.
1200mm Non Woven Fabric Lamination Machine maintenance
Regular cleaning and inspection: In order to ensure the long-term stable operation of the equipment, regular cleaning of the machine is an essential maintenance measure. It is necessary to check the working status of the main components such as the substrate unwinding device, the compounding device and the winding device, and clean up the dust and impurities that may accumulate to prevent them from affecting the operating efficiency of the machine.
Lubrication and refueling: Regularly lubricate the various moving parts of the equipment to reduce friction and extend the service life of the equipment. Special attention should be paid to the lubrication of the transmission system and the motor to ensure that the equipment can run smoothly. When refueling, lubricants that meet the requirements of the equipment should be selected, and excessive refueling should be avoided to cause equipment failure.
Fastener inspection and adjustment: Regularly check whether the various fasteners of the equipment are loose, especially the connecting parts of the unwinding device, the compounding device and the winding device. If looseness is found, it should be tightened in time to prevent the equipment from malfunctioning or being damaged due to looseness when running at high speed.
Tension system calibration: The tension control system of the equipment is crucial to the stability of the composite process. Regularly check the tension control system to ensure its accurate operation. It is necessary to check the sensor, tension control device and electronic control system to ensure the uniformity of tension and prevent material waste or poor composite due to uneven tension.
Maintenance of electrical system: The electrical system of the equipment needs to be regularly checked for aging or damage of power lines, connectors, switches, etc. Especially after the equipment has been in operation for a long time, the electrical system is prone to failure, so a comprehensive inspection of the electronic control system is required to ensure the stable operation of the control system. If necessary, upgrade the system or replace damaged electrical components.
Regular inspection of the transmission system: The transmission system of the equipment is a key part to ensure the normal operation of the equipment, especially when working at high speed, the requirements for the transmission system are very high. It is necessary to regularly check the transmission parts such as gears, belts and motors to ensure that they are not worn, loose or aged, so as to avoid production line shutdowns due to transmission system failures.
Check the operation interface and control system: The operation interface and control system need to be regularly checked to ensure that they function normally and respond in time. In actual operation, if the equipment operation is found to be abnormal, the control system must be checked and adjusted immediately. In particular, electronic control components should be kept clean to prevent external impurities from affecting their normal operation.
Spare parts management and replacement: During the operation of the equipment, some wearing parts may need to be replaced, such as rollers, drive belts and seals. In order to prevent the equipment from shutting down due to damage to certain parts, the spare parts should be checked regularly and replaced in time according to the use of the equipment. In addition, the inventory of spare parts should be maintained to avoid affecting the production progress due to the lack of necessary spare parts.
Foshan Saibang Intelligent Equipmemt Co., Ltd. is located in nanhai District, an important industrial town in Guangdong Province, is a research and development, manufacturing, sales in one of the National High-tech Enterprise. The founding team of the company has been deeply engaged in the new material industry for 15 years, and is committed to the R&D, manufacturing and technical integration of special equipment for the new material & medical and eisai special equipment, providing systematic solutions and technical services for customers. We have over 30 independent intellectual property rights, and after years of experience accumulation, we currently has customers all over the country, Southeast Asia, Europe, and South America.Our products include casting/laminating equipment, coating machine, non-woven special equipment, all kinds of non-standard automation equipment and related mechanical and electrical accessories.
We adhere to the development philosophy of "technology leading, quality winning, service first, and win-win cooperation", with continuous research and development power for the industry to push technical equipment of cutting edge, with stable quality based on competitive global market, with sincere technology service realize the value of customer demand.