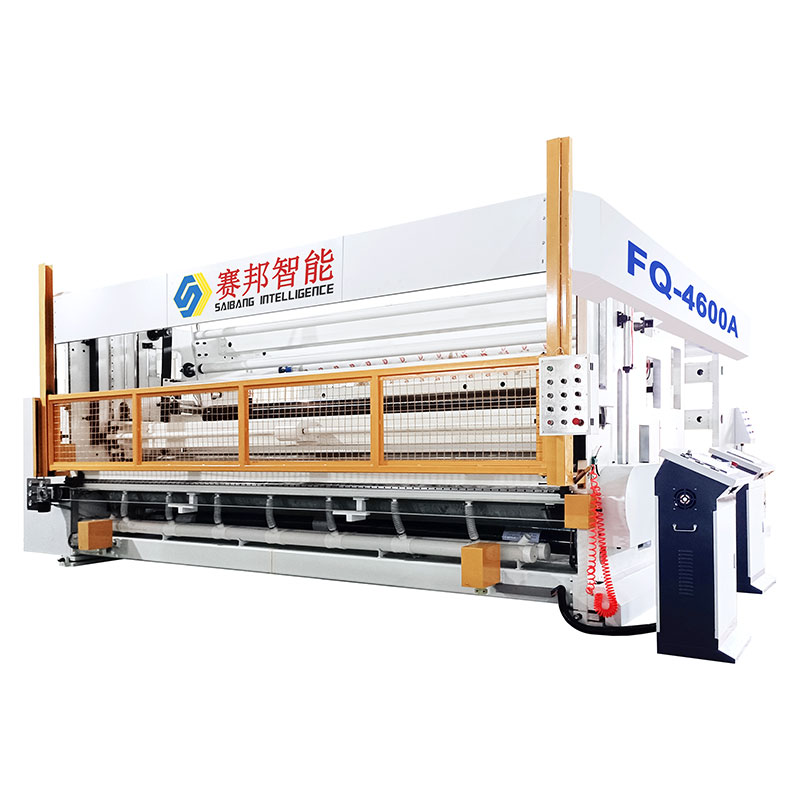
Fabric Slitting Machine uses advanced mechanical structure, precise cutting system and intelligent control system to cut continuous fabric rolls into multiple narrow fabrics that meet production needs according to preset width and length requirements. This equipment can improve the production efficiency of the non-woven fabric production industry, ensure product quality and meet diversified market needs.
4600mm Nonwoven Fabric Slitting Machine parameter
Model: | FQ-4600 |
Brand: | Saibang Intelligence |
Adaptation Materials: | Spunlaced Nonwoven, Spunbonded Nonwoven, Hot Air Nonwoven, Hot Rolled Nonwoven, Melt-Blown Nonwoven, Fluffy Nonwoven, Puffing Paper, Air-Laid Paper,etc. |
Material Width: | 3000-4600mm |
Mechanical Speed: | 800-2000m/min |
Unwinding Diameter: | Φ1300mm |
Winding Diameter: | Φ900mm |
OEM: | OEM/ODM |
4600mm Nonwoven Fabric Slitting Machine features
Significant advantages in wide width adaptation: This fabric slitting machine has strong adaptability in wide width processing and can handle non-woven fabrics and other materials with a wide range of 3000-4600mm. Such a wide range enables it to easily meet the diverse needs of different customers for fabric width. For small enterprises, it can flexibly handle fabrics with narrower widths; for large enterprises, the processing of ultra-wide fabrics is also a piece of cake. For example, in large non-woven fabric production bases, facing the requirements of different orders for width, the equipment can be quickly put into production without complex adjustments, which greatly improves the versatility and market competitiveness of the equipment.
High-speed operation efficiency is excellent: The mechanical speed reaches 800-2000m/min, which is at the leading level in the industry. High-speed operation means higher production efficiency, which can complete more fabric slitting tasks in the same time, effectively shorten the production cycle and reduce production costs. Taking an enterprise that produces tens of tons of non-woven fabrics per day as an example, after using this equipment, the production efficiency has increased by nearly 30%, significantly enhancing the economic benefits and market response speed of the enterprise, enabling the enterprise to meet market demand faster and seize market opportunities.
Outstanding large roll diameter handling capability: The unwinding diameter is Φ1300mm, and the rewinding diameter is Φ900mm. The large roll diameter design allows the equipment to accommodate more fabric materials, reduce the number of frequent roll changes, and improve the continuity and stability of production. At the same time, it helps to reduce the tension fluctuation of the material during unwinding and rewinding, and ensure the stability of the slitting quality. In the long-term continuous production process, the large roll diameter design can ensure that the fabric always maintains stable tension during slitting, avoid wrinkles, breaks and other problems, and ensure the stability of product quality.
Servo drive is precise and stable: The speed synchronization of the whole machine adopts advanced servo drive technology to provide strong guarantee for the stable operation of the equipment. The servo drive system has the characteristics of high precision and high response, and can control the running speed and position of the equipment in real time and accurately, ensuring the excellent synchronization performance of each component. During operation, it can effectively avoid problems such as material stretching and deformation caused by inconsistent speed, and ensure the dimensional accuracy and edge quality of the fabric after slitting. Experimental data shows that after using this servo drive technology, the dimensional accuracy error of fabric slitting can be controlled within ±0.1mm.
Automatic knife arrangement is efficient and accurate: Equipped with an automatic knife arrangement positioning system, it can achieve automatic knife arrangement in 3 minutes, with accurate positioning and improved efficiency. The traditional knife arrangement method requires manual operation, which is time-consuming and labor-intensive and prone to inaccurate positioning. This system can quickly and accurately complete the knife arrangement operation through advanced sensors and control systems, greatly shorten the equipment adjustment time and improve production efficiency. In actual production, the 3-minute automatic knife arrangement time can save nearly half of the time compared with the traditional method, significantly improving the equipment utilization rate.
Convenient human-machine interface operation: The digital human-machine interface is easy to operate. Operators can understand the equipment operation status, production parameters and other information in real time through the intuitive interface, and conveniently set and adjust parameters. At the same time, it has fault diagnosis and alarm functions, which can promptly detect equipment operation problems and provide solutions, reduce the difficulty of operation for operators, and improve the level of production automation.
Fine cutting accuracy control: The cutting system uses high-precision tools and advanced control algorithms to achieve accurate cutting of fabric materials. The cutting width error can be controlled within a very small range to ensure that the fabric after slitting meets strict size requirements. Whether it is for electronic component packaging materials with extremely high dimensional accuracy requirements or clothing accessories with strict standards for edge quality, this equipment can meet their cutting accuracy requirements.
Flexible and accurate tension adjustment: It has an advanced tension adjustment system that can flexibly adjust the tension of the fabric during the slitting process according to the characteristics and thickness of different fabric materials. Through real-time monitoring and feedback control, it ensures that the fabric maintains stable tension throughout the slitting process, avoids problems such as material stretching deformation caused by excessive tension or material wrinkling and deviation caused by too little tension, and ensures the stability and consistency of slitting quality.
Good noise control effect: Noise control factors are fully considered during the design and manufacturing process of the equipment. The use of low-noise transmission components and optimized mechanical structure effectively reduces the noise level during equipment operation. In the production workshop, the noise level of the equipment during operation is significantly lower than that of similar equipment, providing operators with a relatively quiet and comfortable working environment, which is conducive to improving the work efficiency and physical and mental health of operators.
Production of non-woven products: In the field of non-woven products production, such as sanitary products (diapers, sanitary napkins, etc.), medical products (surgical gowns, masks, etc.), and household products (wet wipes, tablecloths, etc.), the fabric slitting machine plays an important role. It can slit wide non-woven fabrics into narrow materials of different specifications to meet the production needs of different products. For example, in the production of diapers, the non-woven fabrics are slit into widths suitable for making the surface layer, side edges, etc. to ensure the comfort and leak-proof performance of the product.
Production of packaging materials: In the packaging materials industry, such as food packaging, industrial packaging and other fields, a large number of fabric materials of different specifications are required. The equipment can slit wide fabrics into suitable widths for making packaging bags, packaging films and other products. Its precise slitting capacity ensures the quality and dimensional accuracy of the packaging materials and improves the beauty and practicality of the packaging.
Production of clothing accessories: Clothing accessories such as linings and linings also need to be slit. The fabric slitting machine can cut wide fabrics into auxiliary materials of different widths and lengths according to the requirements of clothing design, providing high-quality supporting materials for clothing production. At the same time, its high-speed operation and precise positioning characteristics can meet the requirements of clothing production for the timeliness and accuracy of auxiliary material supply.
Automobile interior material production: Automobile interior materials such as seat fabrics and ceiling materials have high requirements for material size accuracy and quality. The equipment can cut wide fabrics into specifications that meet the requirements of automobile interior design, ensuring the splicing effect and overall aesthetics of interior materials. Its stable operating performance and advanced control system can ensure the stability of material quality during the slitting process and reduce the defective rate.
Filter material production: In the field of filter materials, such as air filtration, liquid filtration, etc., fabric materials of different specifications are required. The fabric slitting machine can cut wide filter fabrics into suitable widths for making various filter products. Its precise slitting capacity and high operating efficiency can meet the needs of large-scale and high-quality supply of filter material production.
4600mm Nonwoven Fabric Slitting Machine maintenance
Daily cleaning
Equipment surface cleaning: After the end of production every day, use a clean soft cloth to wipe the surface of the equipment to remove dust, oil and debris. In particular, the operation panel, display screen and other parts of the equipment should be cleaned carefully to prevent dust from entering and affecting the normal operation of the equipment.
Cutting tool cleaning: Clean the cutting tool regularly to remove residue and dirt on the surface of the tool. You can use a special tool cleaner and a soft brush for cleaning. After cleaning, wipe it dry with a clean cloth and apply an appropriate amount of lubricating oil to prevent the tool from rusting.
Transmission parts cleaning: Check and clean the transmission chain, gears, bearings and other transmission parts of the equipment to remove dust and oil on them. You can use compressed air to blow or wipe with a clean cloth to ensure that the transmission parts are clean and well lubricated.
Lubrication maintenance
Lubrication point refueling: According to the equipment's instruction manual, regularly add an appropriate amount of lubricating oil or grease to each lubrication point of the equipment. For the transmission chain, you can use a special chain lubricant and refuel it at regular intervals (such as every week); for bearings and other parts, add grease regularly according to the usage to ensure that the bearings rotate flexibly.
Lubricant replacement: Regularly replace the lubricant in the equipment to ensure the performance and quality of the lubricant. Generally speaking, the lubricant needs to be replaced every certain period of operation (such as 3-6 months) or after a certain mileage. When replacing the lubricant, drain the old oil, wipe the oil chamber with a clean cloth, and then add new lubricant.
Tool maintenance
Tool wear inspection: Regularly check the wear of the cutting tool, use tools such as micrometers to measure the thickness and width of the tool edge, and determine whether the tool needs to be sharpened or replaced. When the tool is worn to a certain extent, it will affect the slitting quality and production efficiency, so it should be handled in time.
Tool sharpening: If the tool is worn but has not yet reached the replacement standard, you can use professional tool sharpening equipment to sharpen the tool. When sharpening, pay attention to the sharpening angle and amount of the tool to ensure that the geometry and angle of the tool meet the requirements. The sharpened tool should be inspected to ensure its sharpness and precision.
Tool installation and adjustment: After replacing or sharpening the tool, the tool should be installed correctly and adjusted. Ensure that the tool and the transmission system of the equipment cooperate well and the slitting effect is stable. When installing the tool, pay attention to the installation direction and tightening strength of the tool to avoid loosening or installation errors of the tool.
Electrical system inspection
Electrical component inspection: Regularly check the electrical components of the equipment, such as contactors, relays, switches, etc., to check whether there are looseness, ablation, aging, etc. If there is a problem with the electrical components, replace them in time to ensure the normal operation of the electrical system.
Electrical circuit inspection: Check the electrical circuit of the equipment to check whether the circuit is damaged, short-circuited, or broken. Especially for the connection parts and plugs and sockets of the equipment, check carefully to avoid the equipment from failing to operate normally due to line failure.
Grounding inspection: Check the grounding of the equipment to ensure that the equipment is well grounded. Poor grounding may cause leakage of the equipment and endanger the safety of the operator. The grounding resistance of the equipment can be measured using a ground resistance tester to ensure that the grounding resistance meets the requirements.
Mechanical component inspection
Transmission component inspection: Regularly check the transmission components of the equipment, such as chains, gears, belts, etc., to check whether there are looseness, wear, breakage, etc. If there is a problem with the transmission components, adjust or replace them in time to ensure the normal operation of the transmission system.
Structural component inspection: Check the structural components of the equipment, such as the frame, beams, columns, etc., to see if there are any deformations or cracks. If any structural component is found to have problems, repair or reinforce it in time to ensure the stability and safety of the equipment.
Tensioning device inspection: Check the tensioning device of the equipment, such as the unwinding tensioning device and the rewinding tensioning device, to ensure that the tensioning device can work normally and ensure the stability of the tension of the fabric during the slitting process. If any tensioning device is found to have problems, adjust or repair it in time.
Foshan Saibang Intelligent Equipmemt Co., Ltd. is located in nanhai District, an important industrial town in Guangdong Province, is a research and development, manufacturing, sales in one of the National High-tech Enterprise. The founding team of the company has been deeply engaged in the new material industry for 15 years, and is committed to the R&D, manufacturing and technical integration of special equipment for the new material & medical and eisai special equipment, providing systematic solutions and technical services for customers. We have over 30 independent intellectual property rights, and after years of experience accumulation, we currently has customers all over the country, Southeast Asia, Europe, and South America.Our products include casting/laminating equipment, coating machine, non-woven special equipment, all kinds of non-standard automation equipment and related mechanical and electrical accessories.
We adhere to the development philosophy of "technology leading, quality winning, service first, and win-win cooperation", with continuous research and development power for the industry to push technical equipment of cutting edge, with stable quality based on competitive global market, with sincere technology service realize the value of customer demand.