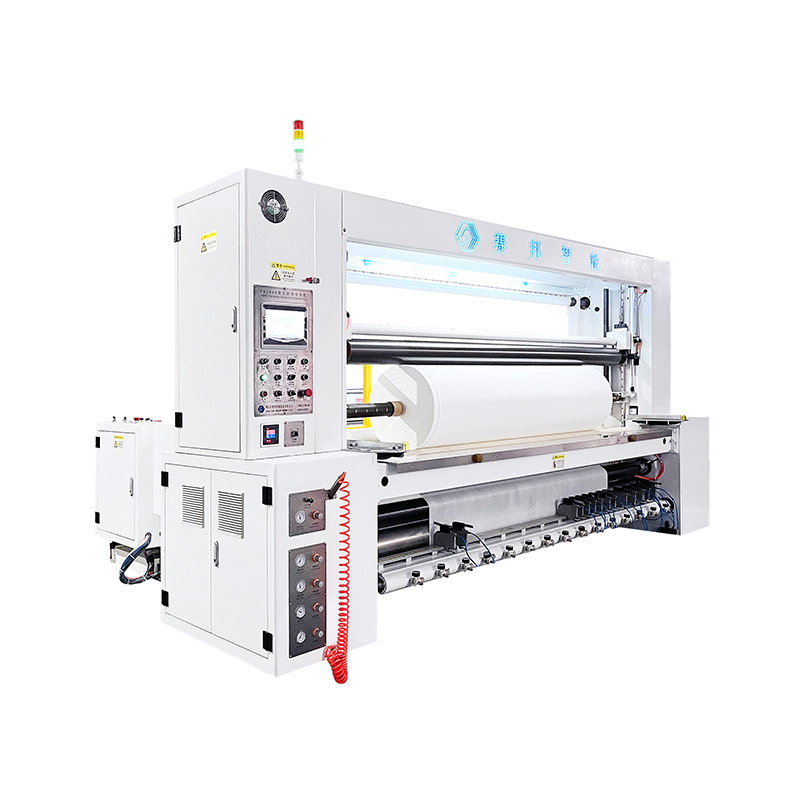
Non Woven Fabric Slitting Machine is an industrial equipment specially used for slitting wide non-woven fabric rolls into narrow rolls. It cuts non-woven fabric materials into rolls of specific width according to production requirements through precise slitting and rewinding functions, ensuring the flatness and size consistency of the material.
3000mm Non Woven Fabric Slitting Machine parameter
Model: | FQ-3000 |
Brand: | Saibang Intelligence |
Adaptation Materials: | Spunlaced Nonwoven, Spunbonded Nonwoven, Hot Air Nonwoven, Hot Rolled Nonwoven, Melt-Blown Nonwoven, Fluffy Nonwoven, Puffing Paper, Air-Laid Paper,etc. |
Material Width: | 2400-3600mm |
Mechanical Speed: | 200-350m/min |
Unwinding Diameter: | Φ1000-1600mm |
Winding Diameter: | Φ1200mm |
OEM: | OEM/ODM |
3000mm Non Woven Fabric Slitting Machine features
High-precision servo drive system: Non Woven Fabric Slitting Machine adopts advanced servo drive technology to ensure the synchronization and accuracy of the whole machine's running speed, and the mechanical speed can reach 200-350m/min. The servo motor adjusts the movement speed of the tool and the coil in real time through a closed-loop control system to avoid stretching or deformation of the material. This high-precision drive system can achieve the error control of the slitting width within a very small range, ensuring the size consistency of each roll of material. At the same time, the servo drive system has a fast response capability and can maintain a stable slitting effect at different production speeds, greatly improving production efficiency.
Modular design: The machine adopts a modular design, and the core functional components (such as slitting unit, rewinding unit, control system, etc.) are independently modularized. This design not only makes the appearance of the whole machine simple and generous, but also greatly improves the convenience of operation and simplicity of maintenance. The modular structure allows users to flexibly adjust the machine configuration according to production needs, such as increasing the number of slitting tools or replacing coil holders of different specifications. In addition, the modular design facilitates troubleshooting and component replacement, reduces downtime, and improves equipment availability.
Intelligent control system: The machine is equipped with an advanced intelligent control system, which usually includes a touch screen operation interface, a PLC (programmable logic controller) and a sensor network. The operator can set parameters such as slitting width, speed, tension, etc. through the touch screen, and the system will automatically adjust the tool position and coil tension to ensure the stability of the slitting process. The sensor monitors the tension, position and speed of the coil in real time. Once an abnormality is detected, the system will immediately issue an alarm and suspend operation to avoid material waste or equipment damage. In addition, the intelligent control system supports data recording and remote monitoring functions, which is convenient for production management and quality traceability.
High stability slitting tool: The machine is equipped with high-precision slitting tools, which are usually made of carbide or ceramic materials to ensure the durability and cutting accuracy of the tool. The tool is tension-adjusted through a hydraulic or pneumatic system and can adapt to non-woven materials of different thicknesses and hardness. The design of the slitting tool also takes into account the characteristics of the material. For example, for soft spunlace non-woven fabrics, the tool will use a blunt cutting method to avoid material tearing; for harder hot-rolled non-woven fabrics, sharp tools are used to achieve clean cutting. The quick replacement design of the tool further improves production efficiency and reduces tool change time.
Efficient rewinding system: The rewinding system of the machine adopts multi-axis synchronous control technology to ensure that the coils after slitting can be rewound evenly to avoid loose or wrinkled coils. The rewinding shaft is usually equipped with an air shaft design to facilitate quick loading and unloading of coils, and the maximum rewinding diameter can reach Φ1200mm. The rewinding system also has an automatic tension control function, which monitors the tension changes of the coils in real time through sensors and automatically adjusts the rewinding speed to ensure the flatness and tightness of the coils. In addition, the rewinding system supports the production needs of various coil diameters and can flexibly adapt to the rewinding of coils of different specifications.
Spunlace Nonwoven Production: Non Woven Fabric Slitting Machine In spunlace nonwoven production, wide webs can be slit into narrow webs suitable for downstream processing, such as medical masks, surgical gowns, wet wipes and other products. The machine's high-precision slitting and rewinding functions ensure the flatness and dimensional consistency of spunlace nonwovens, meeting the strict quality requirements of medical supplies.
Spunbond Nonwoven Production: Non Woven Fabric Slitting Machine In spunbond nonwoven production, the machine can efficiently slit wide webs to ensure that the slit webs meet the specifications of packaging materials or industrial fabrics. The machine's servo drive system and intelligent control system can adapt to the high production speed of spunbond nonwovens while maintaining slitting accuracy and stability.
Hot Air Nonwoven Production: Non Woven Fabric Slitting Machine In hot air nonwoven production, the material can be slit by blunt cutting to avoid material tearing caused by sharp knives. The slit webs can be used to produce products such as warm quilts and mattress fillings. The modular design of the machine allows users to flexibly adjust the slitting parameters according to the characteristics of hot air non-woven fabrics to ensure production efficiency and quality.
Meltblown Fabric Production: Non Woven Fabric Slitting Machine In meltblown fabric production, it can process wide rolls into narrow rolls suitable for mask production through high-precision slitting and rewinding functions. The machine's intelligent control system can monitor the tension and speed of the roll in real time to ensure the stability of the slitting process and meet the strict requirements of meltblown fabrics for dimensional accuracy and flatness.
Fluffy Cotton and Expanded Paper Production: Non Woven Fabric Slitting Machine In the production of fluffy cotton and expanded paper, it can ensure that the slit rolls maintain fluffiness and integrity through optimized slitting knives and rewinding systems. The high stability design of the machine can adapt to the soft characteristics of these materials and avoid deformation or damage of the material during the slitting process.
3000mm Non Woven Fabric Slitting Machine maintenance
Daily cleaning and inspection: After the end of production every day, the machine should be thoroughly cleaned, including removing residual materials on the slitting tool, rewinding shaft and conveyor belt. Regularly check whether there are foreign objects or stains on the surface of the machine to ensure that the machine operating environment is clean. At the same time, check whether the fasteners of the machine are loose. If they are loose, they should be tightened in time. During the cleaning process, special attention should be paid to avoid water or detergents from entering the electrical system to avoid short circuits or damage.
Regular lubrication and maintenance: The transmission parts of the machine (such as gears, bearings, guide rails, etc.) need to be lubricated regularly to reduce wear and extend service life. Add or replace lubricating oil and grease regularly according to the manufacturer's recommendations. When lubricating, ensure that the lubricant is evenly distributed to avoid excessive lubrication that causes contamination of the material. In addition, regularly check the sealing of the lubrication system to ensure that there is no leakage.
Tool maintenance and replacement: The slitting tool is the core component of the machine, and the wear of the tool needs to be checked regularly. For carbide or ceramic tools, if the blade is worn or notched, it should be replaced or re-grinded in time. The cleaning and maintenance of the tool is also very important. After each use, the residual material on the surface of the tool should be removed to avoid damage to the tool due to hardening of the material. The storage of the tool should avoid collision and scratches to ensure the sharpness of the tool.
Electrical system inspection: Regularly check the electrical system of the machine, including components such as wires, plugs, sensors and control panels. Make sure that all electrical connections are firm and not loose or oxidized. Check the working status of the sensor to ensure that it can accurately detect the tension, position and speed of the coil. Clean the dust and dirt of the electrical system regularly to avoid short circuits or failures due to dust accumulation. For aging or damaged wires and components, they should be replaced in time.
System calibration and debugging: Regularly calibrate the slitting system and rewinding system of the machine to ensure the accuracy of the slitting width and rewinding tension. The calibration process should be carried out in accordance with the manufacturer's instruction manual to avoid errors caused by improper operation. When debugging the machine, the parameters should be adjusted step by step, and the slitting and rewinding effects should be observed to ensure stable operation of the machine. After calibration and debugging, record the relevant parameters so that the settings can be quickly restored during subsequent production.
Regular professional maintenance: It is recommended to carry out professional maintenance at least once a year, with the manufacturer or professional technicians conducting a comprehensive inspection and maintenance of the machine. Professional maintenance includes deep cleaning, system inspection, component replacement and performance optimization. Through professional maintenance, potential problems can be discovered in time to avoid equipment downtime or damage due to minor faults. In addition, professional maintenance can also extend the service life of the machine and ensure its long-term stable operation.
Foshan Saibang Intelligent Equipmemt Co., Ltd. is located in nanhai District, an important industrial town in Guangdong Province, is a research and development, manufacturing, sales in one of the National High-tech Enterprise. The founding team of the company has been deeply engaged in the new material industry for 15 years, and is committed to the R&D, manufacturing and technical integration of special equipment for the new material & medical and eisai special equipment, providing systematic solutions and technical services for customers. We have over 30 independent intellectual property rights, and after years of experience accumulation, we currently has customers all over the country, Southeast Asia, Europe, and South America.Our products include casting/laminating equipment, coating machine, non-woven special equipment, all kinds of non-standard automation equipment and related mechanical and electrical accessories.
We adhere to the development philosophy of "technology leading, quality winning, service first, and win-win cooperation", with continuous research and development power for the industry to push technical equipment of cutting edge, with stable quality based on competitive global market, with sincere technology service realize the value of customer demand.